Biological Wastewater Treatment
We offer various wastewater solutions, one of them is biological wastewater treatment technologies with different capacities and according to the needs of our customers. Depending on the size of the treatment plant, we install concrete, steel or package biological treatment systems.
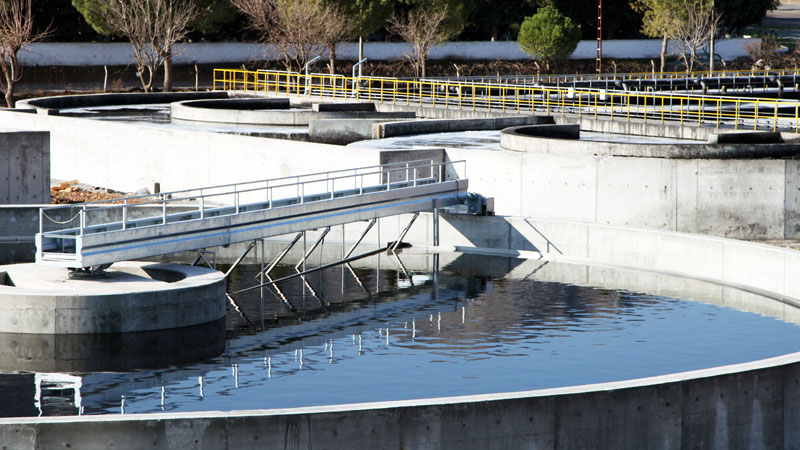
In general definition, biological treatment; organic matter, which cannot be removed in physical and chemical processes in wastewater, is used by microorganisms as a food and energy source and removed from wastewater.
Biological treatment systems can be classified in different ways. These systems, which are classified as aerobic and anaerobic depending on the oxygen in the environment, can also be classified as suspended and bio film processes according to the state of the microorganisms used in the system.
Biological Wastewater Treatment Methods
Sequencing Batch Reactor (SBR)
The sequencing batch reactor (SBR) system is an activated sludge biological treatment process that hybrid systems with plug flow and complete mixed system features.
SBRs are the processes where the aeration, sedimentation and discharge processes take place in the same tank in succession. An SBR is operated in fill, aerate, settle and decant/dischage phases.
In this process, wastewater is taken on activated sludge (bacterial biomass), a diffuser system installed at the base and a blower is used for aeration. Organic substances in waste materials are digested by this activated sludge (biomass) as a food source.
As sedimentation is not carried out in a separate tank, sludge return is not performed. Thus, sludge return pumps are not required.
Sequencing batch reactors can be easily used in the treatment of domestic and industrial wastewater. High amounts of carbon oxidation, nitrification, denitrification and phosphorus removal are provided.
Membrane Bio Reactor (MBR)
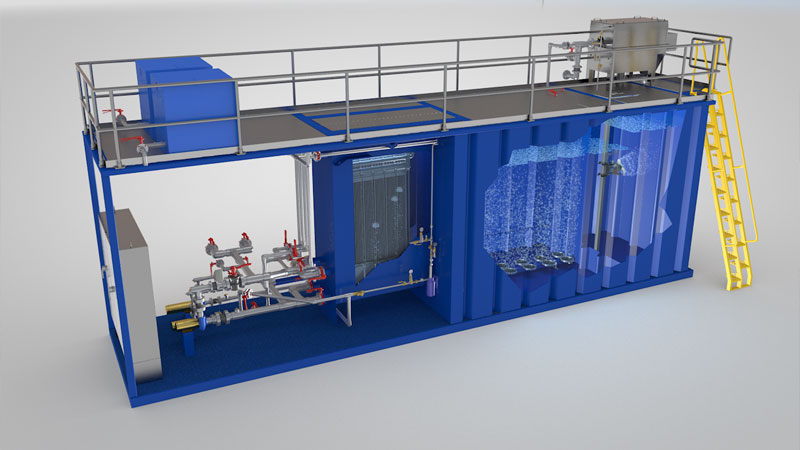
The Membrane Bio Reactor (MBR) is a process to removal of a higher volumetric load in a much smaller area.
The effluent water quality is significantly higher in MBR plants. In conventional systems, the activated sludge – effluent phase is separated by settling. The MBR process does not need a sedimentation tank.
The effluent water quality is significantly higher in MBR plants. In conventional systems, the activated sludge – effluent phase is separated by settling. The MBR process does not need a sedimentation tank.
The factory pore size of manufactured MBR filter is 0,04 micron. However this pore size even gets smaller as the biofilm growth by the activated sludge the promoted and filter surfaces covered. Under steady operation conditions the pore size is expected to be 0,1 micron of which is the level of ultrafiltration where even viruses and bacteria cannot pass through. This high filtration rate not only eliminate the need for a clarifier tank but also ensures the disinfection of the effluent. The MBR enables the system to work at considerably high MLSS – sludge concentrations in the aeration process that in return, smaller aeration volumes are required, no need for final clarifiers, no need for sludge thickeners and no need for further filtration of the effluent. MBR technology requires much smaller footprints. With such advanced filtration, the effluent quality is high and stable; does not fluctuate as in the conventional final clarifiers.
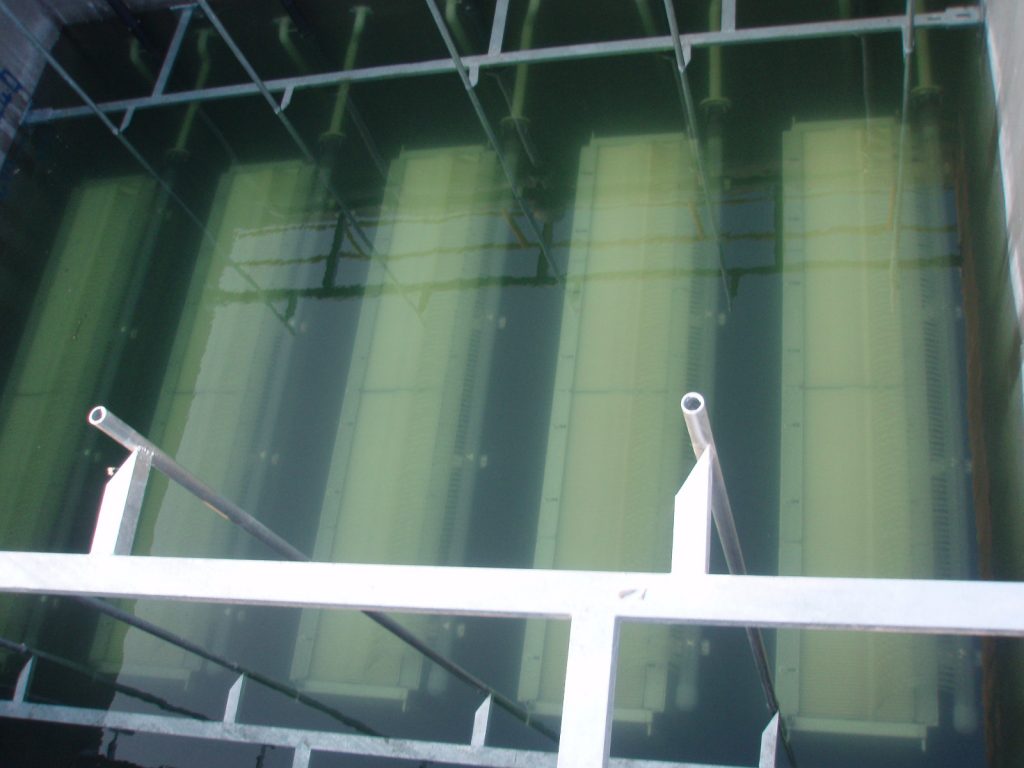
The MBR units are aerated by blowers to control the thickness of the bio-film occurring on the cassettes.There will be a sludge recycling pump for re-circulation to warrant the treatment of the constant incoming waste water flow. Some small amount of activated sludge will daily be removed from the system to keep the sludge age young and efficient by allowing new bacteria to populate.
As the MBR effluent quality will be high and stable, the effluent can be safely used for green irrigation. If preferred a concrete or steel tank for treated water and a suitable irrigation booster can be added to the system by the customer.
Moving Bed Biofilm Reactor (MBBR)
The Moving Bed Biofilm Reactor (MBBR) system is implemented with the use of thousands of special biomass carriers designed to create a very large surface area for biological growth.
MBBR system can be applied in existing facilities. Thus, it provides an increase in facility capacity without the need for additional tanks. The system provides both BOD5 and nitrogen and phosphorus removal, and can be applied in domestic and industrial wastewater treatment plants. Through flexible structure, it is a solution that provides cost advantage in new facilities.
The main difference between MBBR and Conventional Activated Sludge system is to ensure that the suspended growth process and the connected growth process are formed together, and the higher surface area with the same volumes and more organic pollution load can be removed. Especially in capacity increases, more wastewater treatment can be achieved in the same volumes without the need for new tanks.
Advantages:
- High efficiency organic carbon, nitrogen and phosphorus removal
- Flexible design for increased capacity
- Small footprint
- Saving on air demand
- Low investment and operating costs compared to conventional systems
- Stable operating conditions, in cases such as toxicity or overflow, the biofilm is not completely affected and the system will recover faster.
Applications:
- Waste water treatment plant capacity increase
- Wastewater treatment plant improvement applications (higher quality demand in effluent)
- Biological nutrient removal (BNR)
Anaerobic Digestion
The separation of organic substances in wastewater in anaerobic environment and biogas production stage can be summarized as follows:
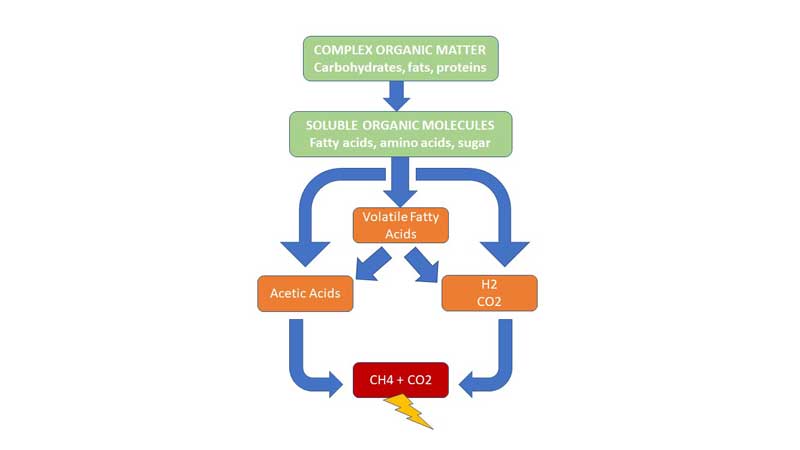
The separation of organic substances in wastewater in anaerobic environment and biogas production stage can be summarized as follows:
Advantages:
- Low operating cost
- Low plant area requirement
- Evaluable biogas production
- Low waste sludge production
There are gases such as Carbon Dioxide (CO2), Methane (CH4), Hydrogen Sulfide (H2S) in the biogas. Of these gases, the calorific value of CH4 gas is 10,000 kcal / m3. The calorific value of biogas is 5000 – 6000 kcal / m3 and this product can be converted into electrical energy by burning it in biogas generators. On the other hand, H2S gas needs to be removed before converting biogas into electrical energy. H2S gas, which is a corrosive gas, damages biogas engines and creates operational problems.